This guide examines the financial feasibility of starting a 150-cow intensive rotational grazing dairy in Missouri. Data presented here reflect costs and conditions as of June 2020. This model was developed using assumptions, costs and benchmarking information from existing Missouri pasture-based dairies and dairy industry experts. While this farm was customized specific to Missouri, it could be adapted to conditions elsewhere.
Farm description
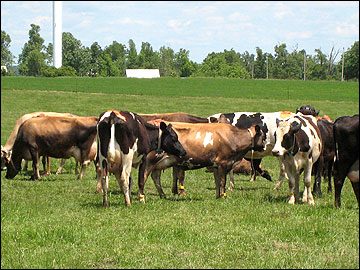
In this model dairy, the farm is a carefully selected 200-acre piece of land purchased specifically for developing a grazing dairy. It is to be located in an area where winter weather conditions and soil types allow cattle to be housed outside all year. The farm is purchased for $3,500 per acre.
- 180 acres for paddocks
- 1 cow per acre for 150 cows
- 30 acres for raising heifers
- 20 acres for farmstead and facilities
- Permanent lanes, water lines and paddocks are established
- No irrigation or winter housing is planned
- The farm is replanted with improved pasture species
Herd management
The beginning herd for this dairy is assumed to include purchased crossbred dairy heifers. The heifers will be purchased with an eye to selecting cattle types best suited for grazing.
Cows are expected to be culled from the herd based on involuntary factors (e.g., death, disease, problem breeders) and voluntary factors (e.g., low milk production, disposition). Projected cow culling rates, death losses and the calving interval for the next five years are listed in Table 1. It is assumed that the average cull rate (excluding deaths) would be 25 percent in the first year and fall to 22 percent in year two. Death loss rate would be 4 percent in all years. The total herd turnover rate would be 29 percent in year one and 26 percent in the remaining years.
Crossbred dairy cows are specified in this grazing dairy system because of their ability to make better use of pasture and their higher reproductivity and overall hybrid vigor. They typically can be purchased for lower prices than Holsteins that are traditionally selected for their high milk production traits. In the model, replacement heifers will be raised on-farm. One-third of the heifers and cows will be bred to beef genetics. Beef cross heifers are sold for $145 each. All bull calves will be sold for $120 each, reflecting a price of mixed crossbred bull calves from dairy and beef sires.
Table 1. Herd turnover and mortality rates.
Description | Year 1 | Year 2 | Year 3 | Year 4 | Year 5 |
---|---|---|---|---|---|
Target herd size (head) | 150 | 150 | 150 | 150 | 150 |
Annual cull rate, excluding deaths (%) | 25 | 22 | 22 | 22 | 22 |
Annual death loss (%) | 4 | 4 | 4 | 4 | 4 |
Calving interval (months) | 14.0 | 13.5 | 12.8 | 12.5 | 12.5 |
Table 2 shows annual milk production estimates and estimated rolling herd average. In the model, 97.5 percent of the total volume of milk is sold, and 2.5 percent from fresh or treated cows is discarded or consumed by calves.
Table 2. Milk production.
Description | Year 1 | Year 2 | Year 3 | Year 4 | Year 5 |
---|---|---|---|---|---|
Pounds per day | 40.0 | 42.0 | 45.0 | 46.0 | 46.0 |
365-day rolling herd average | 12,289 | 12,903 | 13,683 | 13,920 | 13,920 |
Supplementary feeds are designed to complement the characteristics of the pasture forage at a reasonable cost (see Tables 3 and 4). Hay and concentrate are purchased in the dairy model. Ten pounds of concentrate costing $280/ton delivered is fed to each cow in the parlor for the milking group. Five pounds of purchased hay or silage costing $0.10/lb of dry matter is fed as needed throughout the year to the milking group. The dry cow group is being fed 5 pounds of concentrate costing $280/ton and 20 pounds of purchased hay at $0.045/lb as needed throughout the year. Heifer feed costs vary by age, see Table 5 for more detail. Milk replacer and calf starter are used in the initial months before receiving other concentrates, pasture and hay after month 2.
Table 3. Daily milking period feed costs (Cost/cow/day).
Description | Cost/cow/day |
---|---|
Purchased concentrates | $1.40 |
Purchased hay | $0.50 |
Total feed cost | $1.90 |
Table 4. Daily dry cow period feed costs (Cost/cow/day).
Description | Cost/cow/day |
---|---|
Purchased concentrates | $0.70 |
Purchased hay | $0.90 |
Total feed cost | $1.60 |
Table 5. Daily youngstock feed costs (Cost/animal/day).
Description | 0–2 months | 2–6 months | 6–12 months | 12–24 months |
---|---|---|---|---|
Purchased concentrates | $1.70 | $0.48 | $0.60 | $0.72 |
Purchased hay | $0.00 | $0.06 | $0.35 | $0.49 |
Total feed cost | $1.70 | $0.54 | $0.95 | $1.21 |
Milk marketing
Financial projections use a farm-level gross milk price of $18.30 per hundredweight (cwt) in the first two years and $18.44 per cwt in the remaining years, including Dairy Margin Coverage payments during low price months. These price levels are considered realistic based on long-term historical milk prices, component levels and expected premiums in Missouri. Marketing costs deducted from the gross milk price in the model include DMC insurance ($0.15/cwt), dairy checkoff ($0.15/cwt), co-op fee ($0.20/cwt) and hauling ($0.85/cwt).
Labor management
A grazing dairy that milks two times daily will ideally plan to spend no more than 2.5 hours in the parlor per milking. Outsourcing of any necessary forage harvest is used to keep labor costs low. A husband and wife team will be employed at a salary of $42,000 per year, and one part-time employee will be paid $15.50 per hour for 28 hours per week. Benefits cost for labor include only the employer’s share of Social Security and Medicare taxes. Table 6 presents a labor summary. A 2 percent inflation rate is built into labor and select operating expenses.
Table 6. Labor summary.
Description | Year 1 | Year 2 | Year 3 | Year 4 | Year 5 |
---|---|---|---|---|---|
Full-time equivalents (FTEs) (from labor hours) | 2.8 | 2.8 | 2.8 | 2.8 | 2.8 |
Pounds milk per FTE | 646,186 | 673,969 | 714,683 | 727,051 | 727,051 |
Annual benefits | 4,939 | 5,038 | 5,139 | 5,242 | 5,347 |
Total hourly labor | 22,568 | 23,019 | 23,480 | 23,949 | 24,428 |
Total salaried labor | 42,000 | 42,840 | 43,697 | 44,571 | 45,462 |
Total labor cost | 69,507 | 70,898 | 72,316 | 73,762 | 75,237 |
Capital investments
Capital investments for this start-up operation are listed in Table 7. These investments include land, real estate, machinery, equipment and livestock. The total capital invested in the dairy will be $1,327,996 ($8,853 per cow). This includes all the minimum components necessary to make the dairy operational.
Table 7. Capital investments.
Description | Quantity | Cost/Unit | Total |
---|---|---|---|
Land | 200 acres | $3,500 | $700,000 |
Dairy cows | 150 cows | $1,100 | $165,000 |
Heifers (1 year old) | 43 heifers | $400 | 17,200 |
Buildings and farm setup | |||
Milking parlor, equipment, tank, holding area and office | 24 stalls | $7,000 | $168,000 |
Manure storage | $40,000 | ||
Feed bins (15 tons each) | 2 bins | $7,000 | $14,000 |
Hay barn and equipment storage | 5,000 ft | $10 | $50,000 |
Lanes | 9,504 ft | $2.00 | $19,008 |
Watering system (without well and pump) | 9,504 ft | $2.00 | $19,008 |
Fencing and paddock setup | 34,200 ft | $0.90 | $30,780 |
Establishing new forages (fertilizer, seed, tillage) | 180 acres | $150.00 | $27,000 |
Machinery and equipment | |||
Tractor (100 HP with loader) | 1 | $28,500 | $28,500 |
Pickup truck | 1 | $15,000 | $15,000 |
ATV | 1 | $5,000 | $5,000 |
Clipper mower | 1 | $5,000 | $5,000 |
Silage feeding equipment | 1 | $12,000 | $12,000 |
Other farm equipment | $12,500 | ||
Total investment | $1,327,996 | ||
Investment per cow | $8,853 |
The financial success of grazing dairies depends upon keeping the capital investment and the operating expenses low. Careful farm selection is critical to minimize the investment needed and to enable low operating costs. To avoid investments in livestock housing, the farm site must have well-drained soils. To keep feed costs low, the dairy needs mostly open ground with productive soils that can be managed for high-producing pastures that can be planted with annual forage and improved perennial forage varieties.
Investments in the milking center include a milking parlor, milking equipment, holding area, utility room, milk room, rest rooms and tanks. Milking equipment includes parabone stalls designed for rapid cow flow, a flush system for the parlor, automatic take-offs, plate cooler with chilled water and a heater. The parlor is assumed to be a swing-12 parabone parlor with automatic take-offs. The basic philosophy of most graziers carries over to the milking parlor. They want a facility that is both inexpensive and efficient and can be updated or improved as cash flow permits. Parabone swing parlors were used to promote production efficiency by emphasizing cow comfort, cow movement and efficient use of labor. This does not suggest other parlors will not work, but cost and efficiency must always be always considered.
Permanent lanes, water lines and paddocks are established in this dairy. Lanes are essential in a pasture-based dairy to move cows easily from pasture to parlor, whether the grazing cell design is fixed or flexible. Constructing raised lanes with adequate drainage capacity and using crushed rock, lime screenings or other stabilizing material reduces annual maintenance needs and keeps cows cleaner and healthier. Electrified 12.5-gauge high-tensile wire is used for perimeter fence and permanent paddock fencing in this dairy system. Water systems include buried water lines and permanently installed stock tanks.
Initial expenses of forage establishment are included in the capital investments. These expenses include fertilizer, seed and tillage. Pastures can be seeded either on a prepared seedbed or no-till drilling, depending on site conditions and crop requirements. Machinery investments include a tractor, pickup, ATV, clipper/rotary mower, silage feed wagon and other farm equipment. Other facility investments include equipment storage, hay barn and feed bins.
Financial analysis and statements
The 150-cow model dairy will gross $372,745 per year in milk and young stock sales. This farm will have a net income of $32,921 after all operating costs, labor and depreciation are deducted (see Tables 8–11 for financial measurements and statements). On a per cow basis, this is a gross operating income of $2,485 per cow and a net operating income of $219 per cow after labor and depreciation are deducted.
The model represents a dairy using 100 percent equity financing with no debt. Although unrealistic, this simplifying assumption helps lenders analyze the free cash flow to determine how much debt the operation will support. Adding net income from operations plus the building and machinery depreciation yields a free cash flow of $64,886 available for principal and interest payments ($32,291 net income + $32,595 depreciation). On a per cow basis, this is equivalent to $436 of cash available for principal and interest payments. This free cash flow estimate assumes no additional cash will be used for family living expenses other than what is already used to pay labor in the dairy.
Table 8. Financial measurements.
Year 1 | Year 2 | Year 3 | Year 4 | Year 5 | |
---|---|---|---|---|---|
Current ratio | 1.51 | 4.67 | 4.67 | 4.67 | 4.67 |
Return on assets | 0.7% | 1.7% | 3.0% | 3.7% | 3.6% |
Operating expense ratio | 83.3% | 80.5% | 76.9% | 75.6% | 76.2% |
Depreciation expense ratio | 14.1% | 13.2% | 12.5% | 12.1% | 12.1% |
Net farm income from operations ratio | 2.6% | 6.3% | 10.6% | 12.2% | 11.7% |
The character of the investments in the dairy reduces a lender’s risk because a high percentage of the initial investment is concentrated in appreciating land and reproducing cattle rather than specialized assets that are harder to liquidate at full value.
Table 9. Dairy enterprise budget for the 150-cow grazing dairy model (5-year average).
Dollars per herd | Dollars per cow | Dollars per cwt | Percent | |
---|---|---|---|---|
INCOME FROM OPERATIONS | ||||
Milk sales | 358,686 | 2,391 | 18.36 | 96.2% |
Sales of young stock and calves | 14,059 | 94 | 0.72 | 3.8% |
Total gross receipts | 372,745 | 2,485 | 19.08 | 100.0% |
OPERATING EXPENSES | ||||
Feed | ||||
Feedstuffs | 134,289 | 895 | 6.87 | 39.5% |
Less feed for heifers | -32,957 | -220 | -1.69 | -9.7% |
Total feed costs | 101,332 | 676 | 5.19 | 29.8% |
Herd replacement costs | ||||
Depreciation—dairy cows | 15,020 | 100 | 0.77 | 4.4% |
Loss on sale of cows | 7,917 | 53 | 0.41 | 2.3% |
Total herd replacement costs | 22,937 | 153 | 1.17 | 6.7% |
Hired labor (including benefits) | 72,344 | 482 | 3.70 | 21.3% |
DHIA1 testing | 3,900 | 26 | 0.20 | 1.1% |
Semen/breeding | 3,750 | 25 | 0.19 | 1.1% |
Real estate/personal property taxes | 3,455 | 23 | 0.18 | 1.0% |
Milk marketing2 | 26,376 | 176 | 1.35 | 7.8% |
Repairs | 14,700 | 98 | 0.75 | 4.3% |
Vet/medicine | 9,750 | 65 | 0.50 | 2.9% |
Parlor supplies | 5,464 | 36 | 0.28 | 1.6% |
Utilities | 7,806 | 52 | 0.40 | 2.3% |
Insurance | 6,245 | 42 | 0.32 | 1.8% |
Fertilizer | 11,592 | 77 | 0.59 | 3.4% |
Seed/spray | 5,152 | 34 | 0.26 | 1.5% |
Custom hire | 4,163 | 28 | 0.21 | 1.2% |
Truck and fuel | 4,000 | 27 | 0.20 | 1.2% |
Fence/water | 4,000 | 27 | 0.20 | 1.2% |
Other expenses | 3,000 | 20 | 0.15 | 0.9% |
Depreciation | 32,595 | 217 | 1.67 | 9.6% |
Less other expenses for raising heifers | -2,738 | -18 | -0.14 | -0.81% |
Total operating expenses | 339,824 | 2,265 | 17.39 | 100.0% |
NET INCOME FROM OPERATIONS | 32,921 | 219 | 1.68 | |
Notes |
Table 10. Pro forma income statement for the 150-cow grazing dairy model.
Year 1 (dollars) | Year 2 (dollars) | Year 3 (dollars) | Year 4 (dollars) | Year 5 (dollars) | 5-year average (dollars) | |
---|---|---|---|---|---|---|
GROSS REVENUE | ||||||
Milk sales | 331,106 | 345,342 | 366,203 | 375,391 | 375,391 | 358,686 |
Calves and heifers sold | 13,088 | 13,573 | 14,315 | 14,949 | 15,094 | 14,204 |
Total gross revenue | 344,194 | 358,915 | 380,519 | 390,340 | 390,485 | 372,890 |
OPERATING EXPENSES | ||||||
Feed | ||||||
Purchased concentrates | 93,312 | 91,914 | 92,575 | 93,270 | 93,528 | 92,920 |
Purchased hay | 41,434 | 40,583 | 41,187 | 41,732 | 41,908 | 41,369 |
Less feed for heifers | -33,229 | -31,072 | -32,479 | -33,785 | -34,219 | -32,957 |
Total feed costs | 101,518 | 101,425 | 101,283 | 101,217 | 101,217 | 101,332 |
Herd replacement costs | ||||||
Depreciation—dairy cows | 15,857 | 14,811 | 14,811 | 14,811 | 14,811 | 15,020 |
Loss on sale of cows | 8,678 | 7,727 | 7,726 | 7,726 | 7,726 | 7,917 |
Total herd replacement costs | 24,536 | 22,538 | 22,537 | 22,537 | 22,537 | 22,937 |
Hired labor (includes benefits) | 69,507 | 70,898 | 72,316 | 73,762 | 75,237 | 72,344 |
DHIA1 testing | 3,900 | 3,900 | 3,900 | 3,900 | 3,900 | 3,900 |
Semen/breeding | 3,750 | 3,750 | 3,750 | 3,750 | 3,750 | 3,750 |
Real estate/personal property taxes | 3,320 | 3,386 | 3,454 | 3,523 | 3,594 | 3,455 |
Milk marketing2 | 24,426 | 25,476 | 27,015 | 27,483 | 27,483 | 26,376 |
Repairs | 14,700 | 14,700 | 14,700 | 14,700 | 14,700 | 14,700 |
Vet/medicine | 9,750 | 9,750 | 9,750 | 9,750 | 9,750 | 9,750 |
Parlor supplies | 5,250 | 5,355 | 5,462 | 5,571 | 5,683 | 5,464 |
Utilities | 7,500 | 7,650 | 7,803 | 7,959 | 8,118 | 7,806 |
Insurance | 6,000 | 6,120 | 6,242 | 6,367 | 6,495 | 6,245 |
Fertilizer | 11,138 | 11,360 | 11,587 | 11,819 | 12,056 | 11,592 |
Seed/spray | 4,950 | 5,049 | 5,150 | 5,253 | 5,358 | 5,152 |
Custom hire | 4,000 | 4,080 | 4,162 | 4,245 | 4,330 | 4,163 |
Truck and fuel | 4,000 | 4,000 | 4,000 | 4,000 | 4,000 | 4,000 |
Fence/water | 4,000 | 4,000 | 4,000 | 4,000 | 4,000 | 4,000 |
Other expenses | 3,000 | 3,000 | 3,000 | 3,000 | 3,000 | 3,000 |
Depreciation (buildings and equipment) | 32,595 | 32,595 | 32,595 | 32,595 | 32,595 | 32,595 |
Less other expenses for raising heifers | -2,737 | -2,589 | -2,709 | -2,813 | -2,844 | -2,738 |
Total operating expenses | 335,103 | 336,444 | 339,998 | 342,619 | 344,957 | 339,824 |
NET INCOME (LOSS) | 9,091 | 22,470 | 40,521 | 47,721 | 45,527 | 33,066 |
Notes 1 Dairy Herd Improvement Association 2 Includes milk hauling, Dairy Margin Coverage (DMC) insurance, federal promotion and cooperative fees. |
Table 11. Pro forma cash flow statement for the 150-cow grazing dairy model.
Year 1 (dollars) | Year 2 (dollars) | Year 3 (dollars) | Year 4 (dollars) | Year 5 (dollars) | 5-year average (dollars) | |
---|---|---|---|---|---|---|
CASH INFLOWS | ||||||
Milk sales | 331,106 | 345,342 | 366,203 | 375,391 | 375,391 | 358,686 |
Livestock sales | 33,713 | 31,723 | 32,465 | 33,099 | 33,244 | 32,849 |
Total cash inflows | 364,819 | 377,065 | 398,669 | 408,490 | 408,635 | 391,535 |
CASH OUTFLOWS | ||||||
Purchased concentrates | 93,312 | 91,914 | 92,575 | 93,270 | 93,528 | 92,920 |
Purchased hay | 41,434 | 40,583 | 41,187 | 41,732 | 41,908 | 41,369 |
Hired labor (including benefits) | 69,507 | 70,898 | 72,316 | 73,762 | 75,237 | 72,344 |
DHIA1 testing | 3,900 | 3,900 | 3,900 | 3,900 | 3,900 | 3,900 |
Semen/breeding | 3,750 | 3,750 | 3,750 | 3,750 | 3,750 | 3,750 |
Real estate/ personal property taxes | 3,320 | 3,386 | 3,454 | 3,523 | 3,594 | 3,455 |
Milk marketing2 | 24,426 | 25,476 | 27,015 | 27,483 | 27,483 | 26,376 |
Repairs | 14,700 | 14,700 | 14,700 | 14,700 | 14,700 | 14,700 |
Vet/medicine | 9,750 | 9,750 | 9,750 | 9,750 | 9,750 | 9,750 |
Parlor supplies | 5,250 | 5,355 | 5,462 | 5,571 | 5,683 | 5,464 |
Utilities | 7,500 | 7,650 | 7,803 | 7,959 | 8,118 | 7,806 |
Insurance | 6,000 | 6,120 | 6,242 | 6,367 | 6,495 | 6,245 |
Fertilizer | 11,138 | 11,360 | 11,587 | 11,819 | 12,056 | 11,592 |
Seed/spray | 4,950 | 5,049 | 5,150 | 5,253 | 5,358 | 5,152 |
Custom hire | 4,000 | 4,080 | 4,162 | 4,245 | 4,330 | 4,163 |
Truck and fuel | 4,000 | 4,000 | 4,000 | 4,000 | 4,000 | 4,000 |
Fence/water | 4,000 | 4,000 | 4,000 | 4,000 | 4,000 | 4,000 |
Other expenses | 3,000 | 3,000 | 3,000 | 3,000 | 3,000 | 3,000 |
Total cash outflows | 313,937 | 314,971 | 320,053 | 324,084 | 326,888 | 319,987 |
NET CASH FLOW | 50,882 | 62,094 | 78,616 | 84,406 | 81,746 | 71,549 |
Notes 1 Dairy Herd Improvement Association 2 Includes milk hauling, Dairy Margin Coverage (DMC) insurance, federal promotion and cooperative fees. |
Original authors
Joe Horner, Ryan Milhollin, Stacey Hamilton, Wayne Prewitt and Tony Rickard