Increasing energy costs have resulted in resurgence in the use of wood as a fuel for home heating. But heating with wood is not for everyone. Here are a few questions you should ask yourself before investing in a wood-burning unit:
- Does it make economic sense?
- How do you properly size and install a wood-burning unit?
- Is burning wood suited to your lifestyle?
- Where will the wood come from?
This guide provides the basic information to help you answer those questions.
The economics of heating with wood
Usable heat is the amount of heat supplied to a home by a heating system. To compare the usable heat for various types of fuels, you must know the available heat value of the fuel and the operating efficiency of the heating system.
Available heat value
The available heat value of fuel is measured in British thermal units (Btu), and each type of fuel has a specific Btu content per unit of fuel. By definition, one Btu is the heat required to raise the temperature of one pound of water one degree Fahrenheit.
Natural gas has a heating value of about 100,000 Btu per 100 cubic feet (CCF). One CCF is also called a therm. Propane has a heating value of about 92,000 Btu per gallon. The heating value of No. 2 heating oil is about 140,000 Btu per gallon. A kilowatt-hour (kwh) of electricity is equivalent to 3,400 Btu.
It is difficult to evaluate available heat value of wood because of the complex process of obtaining heat from wood. Wood combustion occurs in three consecutive, overlapping stages. In the first stage, heat is actually absorbed and water in the wood is evaporated as steam. In the second stage, volatile matter is liberated and burned. The volatiles ignite, burn and give off heat at about 1,000 degrees F. In the third stage, most of the volatile matter has been removed, and the surface of the remaining residue (charcoal) reaches a glowing temperature and burns when brought into contact with oxygen in the air. This combustion exposes additional surface area until the entire mass is consumed, leaving only ash.
Because heat is needed in the first stage of burning wood to remove water, the more water in the wood at the time you place it in your wood-burning unit means less available heat. One pound of oven-dry wood of any hardwood species has an available heat value of about 8,600 Btu. Resinous softwood species, such as shortleaf pine, tend to average slightly higher at 9,050 Btu per oven-dry pound.
Freshly cut Missouri hardwoods commonly have a 75 percent moisture content on an oven-dry basis. That is, every pound of freshly cut wood contains 0.57 pound of dry wood and 0.43 pound of water. Therefore, the total available heat per pound of wood at 75 percent moisture content is 4,900 Btu (0.57 pound x 8,600 Btu/pound).
Air-dried hardwood firewood typically contains about 20 percent moisture, or 0.83 pound of dry wood and 0.17 pound of water. The available heat value is then 7,100 Btu per pound (0.83 pound x 8,600 Btu/pound).
Of course, firewood is normally not sold by the pound. Volume measurements, such as the cord, are more common and are discussed below. On a volume basis, the heavier air-dried wood is, the more heat it will produce. Therefore, a given volume of the heavyweight woods, such as oak or hickory, will produce more heat than the lightweight ones, such as cottonwood and willow.
Wood pellets are a manufactured biomass fuel. They are made from wood waste materials that are condensed into pellets under heat and pressure. Because they have roughly the twice the density of natural wood and low moisture content (6 percent compared with air-dried wood at 20 percent), pellets have a higher energy content than air-dried firewood, roughly 7,750 Btu per pound.
Operating efficiency
The operating efficiency of a heating system is a measure of how effective the system is at transferring the energy in the fuel into usable heat. It is normally given as a percentage. Operating efficiency will vary from unit to unit, depending on such factors as design, operation and maintenance.
The American Society of Heating, Refrigeration, and Air Conditioning Engineers (ASHRAE) Systems Handbook estimates 70 to 80 percent efficiency for fuel-fired equipment. Newer, high-efficiency units may reach efficiencies as high as 95 percent. If you have upgraded your heating system and wish to compare, use the efficiency rating of your system. The conversion of electricity to heat is assumed to be 100 percent efficient.
Depending upon the type of wood-fired heating unit, operating efficiencies may range from 10 to 90 percent.
The conventional fireplace is the most common wood heating unit. Traditional masonry fireplaces, however, are designed more for show and should not be considered heating devices. Traditional fireplaces draw in as much as 300 cubic feet per minute (cfm) of room-heated air for combustion, and then send it straight up the chimney. As a result, this heating unit has a dismal operating efficiency of about 10 percent, and in some cases can even have a negative efficiency!
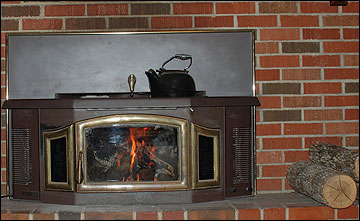
A fireplace insert is designed to fit into an existing conventional fireplace (Figure 1) to increase its operating efficiency, in some cases up to 40 percent. Inserts come in two distinct styles. One style uses a series of hollow C-shaped tubes to circulate room air around the fire. The other style uses an airtight steel firebox similar to an airtight stove. Before choosing this type of wood-heating unit, have a professional installer examine the fireplace and chimney to determine if they are suitable for an insert.
Convective fireplaces are designed to include the fire-viewing benefits of a traditional fireplace with efficiencies of a wood stove. A convective fireplace is a fabricated metal fireplace with a double wall around the firebox. Room air is drawn in through vents under the firebox, heated through a heat exchanger, and sent back into the house either through vents at the top of the fireplace or through ducts leading to nearby rooms. Some of these fireplaces are approved to route heated air to a basement auxiliary fan. The air then travels through ducts to other rooms in the house. A convective fireplace needs a dedicated supply of outside air for combustion; otherwise its operating efficiency is reduced to little better than a traditional fireplace. These units have an average operating efficiency of 40 percent.
Airtight stoves have an airtight firebox with carefully sealed joints and door openings. The only air allowed into the firebox must come through the air inlet openings. These openings are carefully controlled by dampers. Because the amount of air entering the firebox can be controlled, airtight stoves have relatively high operating efficiency, averaging 55 percent. Franklin stoves, parlor stoves and old-fashioned potbelly stoves are examples of non-airtight stoves. These wood-burning units have operating efficiencies of about 25 percent.
An advanced combustion wood stove has several components that help it burn combustible gases, as well as particulates, before they can exit the chimney. Components include a metal channel that heats secondary air and feeds it into the stove above the fire. This heated oxygen helps burn the volatile gases above the flames without slowing combustion. Many older stoves have only one air source below the wood; the secondary air source in advanced combustion stoves offers oxygen to the volatile gases escaping above the fire. With enough oxygen, the heated gases burn as well. In addition, the firebox is insulated, which reflects heat back to it, ensuring that the turbulent gases stay hot enough to burn. New advanced combustion stoves have advertised efficiencies of 60 to 72 percent.
Centralized wood heaters use wood gasification technology that burns both the wood fuel and the associated combustible gases, making them up to 80 percent efficient. In addition, systems are available that can switch to oil or gas if the fire goes out.
Masonry heaters, also known as a Russian, Siberian or Finnish fireplaces, include a firebox, a large masonry mass (such as bricks) and long, twisting smoke channels that run through the masonry mass. The firebox is lined with firebrick, refractory concrete or similar materials that can handle temperatures of over 2,000 degrees F (1,093 degrees C). A small, hot fire built once or twice a day releases heated gases into the long masonry heat tunnels. The masonry absorbs the heat and then slowly releases it into the house over 12 to 20 hours. The only disadvantage of a masonry heater is that it cannot provide heat quickly from a cold start. Masonry heaters commonly reach a combustion efficiency of 90 percent.
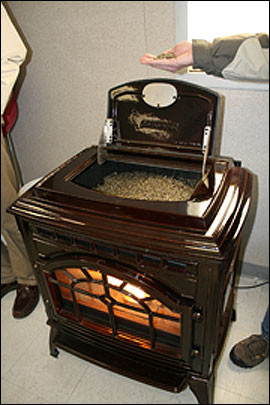
A pellet stove burns small, wood pellets that look like rabbit feed (Figure 2). The pellets are stored in a hopper until they are needed for burning. A feeder device, which turns like a large screw, drops a few pellets at a time into the combustion chamber for burning. How quickly pellets are fed to the burner determines the heat output. More advanced models have a small computer and thermostat to govern the pellet feed rate. These heating units have combustion efficiencies as high as 85 percent.
Fuel replacement cost
Table 1 shows the amount of various replacement fuels needed to equal the amount of usable heat released from burning one cord of air-dried (to 20 percent moisture content) hardwood firewood, containing 80 solid cubic feet of wood with an average density of 40 pounds per cubic foot (similar to a cord of oak or hickory firewood), in a wood-burning unit with an operating efficiency of 50 percent.
To determine the economic relationship of wood to fossil fuels and electricity, simply multiply the unit cost of the replacement fuel by the appropriate energy equivalent. This calculation gives the approximate value of wood as compared with fossil fuels and electricity on a Btu basis, at the stated operating efficiencies. For example, at $8 per therm, the amount of natural gas needed to provide the usable heat equivalent of a cord of firewood would cost $120. Similarly, at $2 per gallon or $0.08 per kwh, it would cost $330 or $267 to purchase an equivalent amount of usable heat from propane or electricity, respectively.
Keep in mind that these are fuel costs only. This basic economic analysis does not consider the purchase price (and any related financing), installation or any maintenance costs of the heating unit.
Table 1. Amounts of various fossil fuels and electricity needed to equal the usable heat released from one cord of firewood.1
Replacement fuel | Energy equivalent |
---|---|
No. 2 heating oil2 | 108 gal |
Propane3 | 165 gal |
Natural gas4 | 150 therms |
Electricity5 | 3,341 kwh |
1. Based on 11.4 million available Btu/cord of hardwood firewood and 50% unit operating efficiency. One cord contains 80 solid cubic feet of wood, air-dried to 20% moisture content with an average density of 40 lb/ft3. 2. Based on 140,000 available Btu/gal and 75% unit operating efficiency. 3. Based on 92,000 available Btu/gal and 75% unit operating efficiency. 4. Based on 1 million available Btu/therm and 75% unit operating efficiency. 5. Based on 3,400 available Btu/kwh and 100% unit operating efficiency. |
Sizing and installing a heating unit
Today’s wood-fired heating units are clean burning, efficient and powerful enough to heat an average-size, modern home. To best provide these benefits, however, a unit must be the proper size for the space to be heated. When a wood-fired unit is too big, people tend to burn fires at a low smolder to avoid overheating, which wastes fuel and is one of the biggest causes of air pollution. When purchasing a heating unit, talk with the dealer about size requirements. Generally, a unit rated at 60,000 Btu can heat up to a 2,000-square-foot home, and a unit rated at 42,000 Btu can heat up to a 1,300-square-foot space.
Before installing a wood-fired heating system, contact your local building codes department, state energy office or state environmental agency about wood-burning regulations that apply in your area. Although cleaner burning than ever before, wood-fired heating units still may emit large quantities of air pollutants, including nitrogen oxides, carbon monoxide, organic gases and particulate matter, many of which have adverse health effects. In many urban and rural areas, smoke from wood burning is a major contributor to air pollution. Because of this, some municipalities restrict wood-fired heating units when the local air quality reaches unacceptable levels; others restrict or ban the installation of wood-burning units in new construction.
If you have an older wood-burning unit, you might want to upgrade to one of the newer units certified by the U.S. Environmental Protection Agency (EPA). All wood-fired heating units sold since 1988 should bear an EPA certification sticker, which is normally located on the back of the unit. These newer units are designed to burn combustible gases and soot particles typically found in the smoke, thereby cleaning the exhaust gas while generating more heat. High-efficiency units not only have lower emissions but also are often safer because complete combustion helps prevent a buildup of flammable chimney deposits called creosote.
For safety and to maximize efficiency, consider having a professional install your wood-burning unit. A professional will evaluate everything from the chimney to floor protection and can help select the best unit to heat your home.
Other factors to consider
In addition to economics, you should consider other factors before choosing to heat your home with wood. On the positive side, access to a woodlot or some other readily available wood supply will give you a feeling of self-sufficiency. Even if you have to pay someone else for your wood, most likely it will be a woodlot owner or firewood supplier in your area and not some large energy supplier.
On the negative side, there are many inconveniences associated with burning wood. For example:
- Wood is a bulky material, and room for storage is required.
- Dirt, bark and other debris fall from the wood as it is moved through the house or basement and into the wood-burning unit. More dust may also accumulate in the house from burning wood than from burning fossil fuels or using electricity.
- Wood-burning units need frequent refueling. You cannot turn on a valve or switch and then walk away.
- Wood-burning units tend to build up heat and then cool off as the fire dies down. It is difficult to maintain a constant temperature.
- Dried wood burns most efficiently. A full summer is required to thoroughly prepare wood for use after it is cut to length.
- Cutting wood is time-consuming and hard, physical work.
- Much handling is involved in transporting wood from the tree or woodland to the wood-burning unit.
Of course, many of the negative aspects are mitigated if you choose to heat with wood pellets. Pellet stoves have a fuel hopper to store the pellets until they are needed for burning. Most hoppers hold 35 to 130 pounds of fuel, which will last a day or more under normal operating conditions. The exhaust gases are vented by way of a small flue pipe that can be directed out a sidewall or up through the roof.
Pellet stoves usually require refueling only once a day, and because the fuel is compressed and bagged, the operator does not have to lift heavy, dirty logs. Most pellet appliance exteriors (except glass doors) stay relatively cool while operating, reducing the risk of accidental burns. Because pellet stoves burn fuel so completely, very little creosote builds up in the flue, posing less of a fire hazard.
Unfortunately, pellet stoves are more complex than other wood-heating units and have expensive components that can break down. They also require electricity to run fans, controls and pellet feeders. Unless the stove has a back-up power supply, the loss of electric power results in no heat.
Where will the wood come from?
Buy it
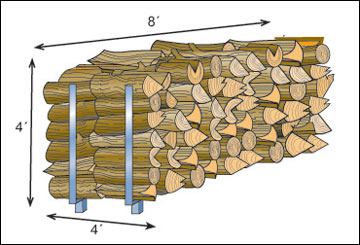
As mentioned earlier, a common measure of small-diameter wood suitable for fuel is the standard cord. A standard cord is a stack of wood, bark and air spaces 4 feet high, 4 feet wide, and 8 feet long for a total volume of 128 cubic feet (Figure 3). The amount of wood received will vary somewhat in the way it is stacked. A cord of loosely piled wood will contain less wood than a more uniformly stacked pile.
Actual volume of solid wood in a cord varies from 65 cubic feet for small, crooked sticks, increasing with the size and straightness of the sticks up to about 90 cubic feet. Average for the Midwest region is about 80 cubic feet.
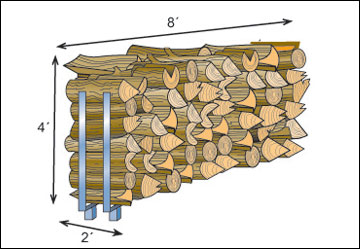
Firewood is frequently sold in quantities less than a cord. A seller may deliver a “face cord” or “rick.” A rick is a stack of wood 4 feet high, 8 feet long and a width that varies usually between 18 and 24 inches (Figure 4). Ricks are often sold as cords. So, buyer beware!
Wood is also sold by the pickup truckload. Trucks with a standard bed measuring about 5.5 feet wide by 8 feet long by 20 inches deep, loaded level with the sides will contain about one-half cord. Trucks with smaller beds 4 feet wide by 6 feet long by 20 inches deep will contain about one-third cord when filled level with the sides of the bed.
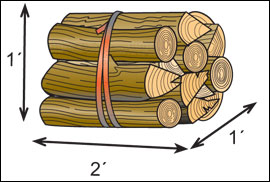
Another element of the wood business is the firewood bundle, often seen at supermarkets. Seasoned oak or other dried hardwood weighs about 3,600 pounds per cord. Bundles weighing about 36 pounds represent about 1/100 cord. Another measuring method may be by bundle size. For example, a bundle 1 foot by 1 foot by 2 feet would be 2 cubic feet, or 1/64 cord (Figure 5). Firewood bundles purchased at the supermarket may be appropriate for the occasional fire in a conventional fireplace, but it is definitely the most expensive way to purchase wood fuel for heating your home!
When you purchase firewood from another party, you will likely buy a mix of various hardwood species. This makes it difficult to predict the available heat value of the firewood and is one reason why we used a general heat value to compare wood with fossil fuels and electricity earlier in this guide.
However, of more importance and something you can control, is the relative moisture content of the wood you buy. Remember that dry wood has a higher heat value than fresh-cut (or green) wood. When purchasing firewood, look at the ends of the pieces to determine if the wood is dry. Seasoning checks (open splits) will be clearly evident on the ends of at least partially dried wood. These “checks” result from the natural shrinkage of wood as it dries. If the wood has been seasoned outside, it will be somewhat discolored. It should not smell sappy.
Lastly, the wood should be hard and sound. Decayed wood has a lower heat value and, when dried, will feel light and burn rapidly.
Missouri law requires that in the sale of firewood a bill of sale be provided showing the name and address of the purchaser and the seller and the cords or fractions of a cord involved in the sale.
Cut it yourself
If you cut wood wisely, the remaining woodland will be more productive. Owners frequently cut the straight, well-pruned trees for firewood because they split easier than crooked trees with many limbs. This practice, coupled with leaving low-quality trees, reduces woodlots to junk lots.
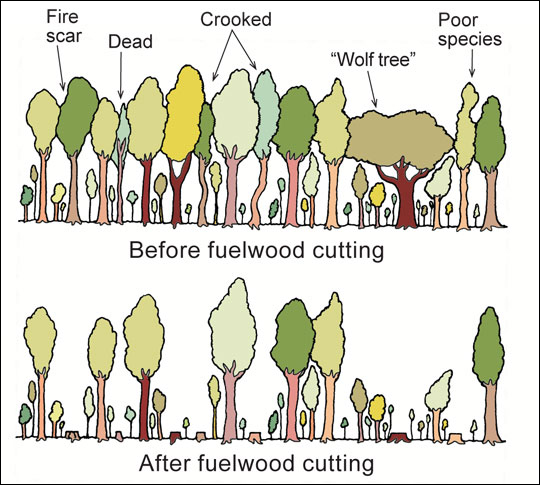
Cut only those trees that, when removed, will give more room for growth to the most desirable trees in the woodlot. This forest improvement practice can produce an abundance of firewood and will increase the growth rate and ultimate value of the remaining trees (Figure 6).
Following are the most important classes of material you should use for fuel wood (one set of rules does not exactly fit every situation):
- Sound dead trees and logging wastes, such as tops and large limbs
- Diseased or insect-infested trees (if the wood can be burned in a short period of time to prevent pest spreading)
- Brushy, crooked or broken hardwoods
- Trees that have been seriously overtopped and stunted by others
- “Wolf” trees (those with unusually large spreading tops occupying excessive space)
- Undesirable species
Before felling, mark trees to be cut with brightly colored plastic flagging tape. Flagging tape is inexpensive and can be purchased at most home improvement centers or hardware stores. This will help you envision what your woodlot will look like after the trees are cut. If you think you are removing too many trees, go back and make adjustments. The old carpenter’s rule, “Measure twice, cut once” makes good sense also in your woodlot!
In contrast to buying firewood, cutting from your woodlot gives you more control over the types (species) of trees that you use for fuel. Table 2 gives some general ratings to help guide you in deciding which trees to burn in your wood-burning unit.
To get the most heat value, allow wood to dry following cutting and splitting. This usually requires several months. Most dense hardwoods require at least one year to season fully.
The more wood surface exposed to air, the faster it dries. Stack the wood in loose piles off the ground. The best place is a storage area exposed to sunlight. Covered storage, open on the sides, helps prevent rewetting from rain or snow.
Table 2. Relative ratings for firewood.
Species | Relative amount of heat | Easy to burn? | Easy to split? | Have heavy smoke? | Pop or throw sparks? | General rating and remarks |
---|---|---|---|---|---|---|
Hardwood trees | ||||||
ash, hard maple, dogwood, mulberry, pecan, ironwood | High | Easy | Easy | No | No | Excellent |
beech, birch | High | Easy | Easy | No | No | Excellent |
red oak, white oak | High | Fair | Fair | No | No | Excellent |
hickory, hard maple | High | Easy | Difficult | No | No | Excellent; hickory hottest burning common hardwood |
Osage-orange (hedge) | Very high | Fair | Difficult | Moderate | Yes | Very good, except will spark if burning green |
soft maple | Medium | Easy | Difficult | No | No | Good |
cherry | Medium | Fair | Easy | No | Some | Good |
walnut | Medium | Easy | Easy | No | No | Good |
cherry, hackberry, soft maple, walnut | Medium | Yes | Yes | No | No | Good |
blackgum, elm, sycamore | Medium | Medium | Difficult | Moderate | No | Fair; too much water when green |
aspen | Low | Easy | Easy | Medium | No | Poor |
basswood, cottonwood, yellow-poplar, willow | Low | Easy | Easy | Moderate | Some | Fair; good for kindling |
boxelder | Low | Easy | Easy | Medium | No | Poor; gives off foul odor |
Softwood trees | ||||||
southern yellow pine | High | Easy | Easy | Some | Some | Fair; high sap may lead to creosote build-up |
eastern redcedar | Medium | Easy | Easy | Moderate | Yes | Fair; good for kindling |
cypress | Medium | Medium | Easy | Moderate | No | Fair; high sap may lead to creosote build-up |
Insects in firewood
Today, our forests and woodlots are threatened by a wide array of insects and disease-causing pathogens. Most of the forest pests live just below the bark. For both foreign and domestic pests, one of the major pathways responsible for their spread is through the movement of firewood, whether it is used to heat your home or to provide the aesthetic beauty of a campfire.
Please contact your state agriculture or forestry agency to learn the latest threats to the forests and woodlands in your region. More important, find out if there are any quarantines restricting the movement of firewood in your area. The best advice is to buy or cut your wood locally, and burn it locally.
Poisonous wood?
Small pieces of wood, or kindling, in combination with paper are frequently used to get a wood fire started. Leftover scraps of lumber from building and construction sites are a convenient source of kindling materials. However, some of the wood frequently used in building is treated with chemicals to prevent decay and insect attack and should not be used for home fuel because of the poisonous nature of the preservatives. Wood treated with the common salt type preservatives is usually light to bright green or light brown in color. Other preservatives leave the wood oily. Creosote leaves wood dark brown to black.
Wood ashes
Wood ashes have some value as a lawn and garden fertilizer. Native Midwest woods seldom contain over 1 percent ash on an oven-dry basis, or about 36 pounds per cord of dense, air-dried wood. This ash consists of 50 to 70 percent calcium or lime, 6 to 8 percent potassium, insignificant amounts of phosphorous, and no nitrogen. The use of 25 pounds of wood ash per 1,000 square feet on home gardens will meet potassium requirements and help maintain a soil pH of 6 to 7 when there is a trend toward acidic conditions.
In summary
Wood can provide a source of home heat at considerable savings compared with fossil fuels and electricity if a source is readily available for little or no cost and if the individual has the equipment and physical energy to cut and transport it. If cut and delivered wood has to be purchased, considerably less savings are evident. Wood varies tremendously in its heating ability; the higher density hardwoods are the best to burn. Burning wood for home heat, unlike fossil fuels and electricity, involves a lot of work. But wood fuel from properly managed woodlots represents a renewable energy resource that can benefit both the homeowner and the forest.